Выбор намотки и вида плетения для электронных сигарет. Проволока в изготовлении бижутерии
наверхРано или поздно любой вейпер узнаёт о возможности мотать собственные спирали на атомайзер и задумывается над тем, зачем же, собственно, это всё нужно, ведь можно просто купить новую «голову». Необходимость создания собственных намоток сегодня не так велика, как раньше, но вейперы всё ещё могут получать значительные преимущества от собственных спиралей.
Во-первых, самостоятельно создавая спираль, можно достичь целевого сопротивления, отличного от тех, что выпускают фабрично. К примеру, для клиромайзера Kanger SubTank существуют стандартные головы для сабомного парения (0,5 Ома) и сигаретной затяжки (1,5 Ома). Если же вы захотите добиться минимального сопротивления, например, 0,1 Ома, либо, наоборот, установить спираль с большим сопротивлением под сигаретную затяжку (1,8 Ома), то вам придётся или менять клиромайзер, или создавать собственную намотку.
Во-вторых, набравшись достаточно опыта, вы сможете влиять на температуру пара, удар по горлу и другие ощущения от парения.
В-третьих, собственные намотки для электронных сигарет позволяют экономить, так как расходные материалы стоят меньше, чем собранный на фабрике испаритель. В долгосрочной перспективе выгода может стать весьма заметной.
Для создания намотки понадобится обслуживаемый атомайзер, имеющий специальную базу под установку собственной спирали. Как правило, такая база обозначается аббревиатурой RBA или RTA — rebuildable atomizer и rebuildable tank atomizer соответственно; RDTA — rebuildable dripping tank atomizer (дрипка с баком). К примеру, упомянутый уже SubTank позволяет использовать RBA базу. В рамках данной статьи мы рассмотрим в первую очередь именно Субтанк, так как это одна из самых популярных моделей, и многие вейперы начинают мотать именно с неё.
Атомайзеры для намоток
наверхПри выборе обслуживаемого атомайзера можно обратиться к опыту вейпинга. Среди сообщества популярны следующие модели:
Kanger SubTank — уже «прорекламированное» устройство, ставшее одним из первых популярных сабомных клиромайзеров. Отличается высоким качеством и «неубиваемостью», а также возможностью использования как заводских спиралей, так и самостоятельных намоток, за что его и полюбили вейперы. Стоит упомянуть и его новую модификацию TopTank — модель с верхней заправкой, которую не нужно откручивать от мода, чтобы залить жидкость;
Kayfun — распространённая в России марка, производящая только обслуживаемые клиры;
Billow v2 — клир, отличающийся от предыдущих возможностью установки двух спиралей, а не одной;
Zephyrus (Zephyrus v2) — тоже двухспиральный клиромайзер высокого качества, полюбившийся отечественным вейперам за схожую с SubTank универсальность — возможность работы с собственными намотками и заводскими «головами»;
Velocity — дрипка, то есть конструкция, не подразумевающая хранение жидкости, а прямое закапывание «жижи» на спираль. Такой вид парения сложнее и менее комфортен — одного закапывания хватает в среднем всего на один «перекур». Но зато получается очень много пара и вкуса.
Материалы для намоток
наверхПо сути, кроме самого обслуживаемого атомайзера вейперу понадобится всего две вещи: проволока и вата. Проволока станет спиралью, а вата фитилём, который будет смачиваться и под воздействием нагрева спирали и поступающего воздуха при затяжке «выдавать» пар. На сегодняшний день существует несколько вариантов материалов.
Материалы для спирали
- нихром — отличается хорошими эксплуатационными качествами, удобен в намотке и недорого стоит;
- кантал — он же фехраль, и второе название даже более правильное, ведь «кантал» — это имя производителя материала. Аналог нихрома, но не имеет в своём составе никеля, из-за чего меньше стоит, меньше служит и не так удобен в эксплуатации, ибо скручивается и пружинит. Последний недостаток устраняется путём нагрева, но об этом ниже. За сочетание цены и качества кантал считается наиболее популярным материалом;
- нержавейка — дешёвый и доступный материал, обладающий большим сроком службы. Не очень удобен в намотке, поэтому используется не часто. Тем не менее, в последнее время стали появляться устройства с температурным контролем (ТК), функционирующие на нержавейке, поэтому популярность материала растёт, ведь он может работать и в режиме ТК, и вариватта одинаково хорошо. При этом в отличие от титана и никеля с нержавейкой легко можно создать намотку с высоким сопротивлением (примерно 1 Ом);
- никель — дорогой материал для устройств с температурным контролем. Для новичков не представляет ценности, так как слишком дорог для «опытов»;
- титан — аналог никеля, с тем лишь отличием, что не выделяет вредных веществ при перегреве (такая же проблема есть и у кантала с нихромом). Перегревается ли никель в устройствах с ТК выше «порога опасности» в 600℃ — пока что спорный вопрос, ведь моды «держат» максимальную температуру в пределах 350℃. Из-за сохраняющейся потенциальной опасности многие вейперы уже переходят на титан для уверенности.
Материалы изготовления фитиля
- кремнеземный шнур — устаревший материал, практически не использующийся сегодня. Даёт меньше пара и вкуса, чем другие, быстро загрязняется и относительно плохо проводит жидкость;
- вата — обязательно нестерильная, иначе при парении будет «привкус больницы». Очень дешёвый и доступный в любом уголке мира материал, приобрести который можно в любой аптеке или супермаркете. Подойдут даже ватные диски;
- японский хлопок — лучший материал на данный момент, не дающий привкуса и лёгкий в использовании. Правда, для начинающего вейпера может показаться дорогим.
Сопротивление намотки
наверхОсновная характеристика созданной намотки — её сопротивление. К примеру, намотка на Субтанк может быть как стандартных значений вроде 1,2 Ома, 0,5 Ома, то есть аналогом продающихся готовых испарителей, так и 0,7 Ома, 0,3 Ома и так далее. Сопротивление зависит от нескольких признаков:
- длина спирали — она же количество колец. Чем больший «путь» нужно пройти току, тем больше сопротивление;
- толщина — чем больше толщина проволоки, тем ниже сопротивление. Однако наращивать толщину бесконечно нельзя, и уже на 0,4 мм становится сложно создавать кольца. Также на разогрев большой толщины требуется больше энергии, следовательно, увеличивается расход батарейки;
- значение сопротивления материала. Разные материалы значительно отличаются по своему сопротивлению, поэтому количество витков, их диаметр и общая длина спирали также будут отличаться.
При создании намотки следует учитывать, что чем больше витков и их диаметр, тем больше получается площадь нагрева, влияющая, в свою очередь, на температуру и количество пара. Однако нельзя просто «намотать побольше», так как мод может «не потянуть» такую спираль, из-за чего она будет плохо греться, либо банально не поместится в клиромайзер.
Намотка спирали для электронных сигарет должна производиться с учётом законов Ома. В зависимости от используемого аккумулятора последствием неправильной намотки может быть как просто отказ работать (моды с платой), так и выход из строя всего устройства (мехмоды). К примеру, если вы накрутили спираль с сопротивлением 0,5 Ома на свой SubTank, то вам потребуется мод, работающий на более чем 15 Ваттах. Однако на современном рынке редко встречаются моды с 15 Ваттами «на борту», которые «умеют» работать с низкоомными намотками. Поэтому важно, чтобы е-сигарета подходила не только по мощности, но и по поддерживаемому сопротивлению. И, как правило, такие устройства «стартуют» с 30 Ватт. Важен и аккумулятор — он должен быть высокотоковым, чтобы избежать перегрева.
Добиться на малых Ваттах низкого сопротивления можно ещё и на никелевых или титановых намотках, но они могут неправильно работать без температурного контроля и быстро выходить из строя.
- Для получения 0,5 Ом на кантале А1 с толщиной проволоки 0,4 мм потребуется 5,5 витков диаметром 2,25 мм.
- Для получения 0,3 Ом на никеле Ni 200 c толщиной проволоки 0,2 мм потребуется 11,5 витков диаметром 2,5 мм.
Звучит сложно, но в современном мире всё просто благодаря интернету. Многочисленные онлайн-калькуляторы позволяют рассчитать намотку в два счёта, к примеру reprova или coiltoy . Ресурсы предлагают даже приложение для мобильных телефонов.
Сегодня самыми популярными значениями сопротивления являются «сабомные», то есть ниже 1 Ома. Намотки можно создавать вплоть до 0,05 Ома, если вы парите на моде с платой (при условии поддержки такого сопротивления, разумеется), или ещё ниже, если на мехмоде. Благодаря наличию защит такое низкое сопротивление стало безопасным, и вы можете не беспокоиться о возможном замыкании. Также всё ещё популярны «классические» значения 1,2 и 1,6 Ома, которые дают меньше пара, но отлично работают на маломощных е-сигаретах. Такие Омы очень «уважают» любители сигаретной затяжки.
Виды намотки
наверхВсего существует пять основных видов намотки. Вот эти койлы (спирали):
Микрокойл или нанокойл — небольшая спираль, витки которой расположены на минимальном расстоянии друг от друга. Подходит для небольших клиров и выдаёт много пара, так как площадь нагрева у неё больше. Однако при создании такой спирали нужно тщательно следить за отсутствием КЗ;
Обычный койл или спейскойл — слово space в нём означает не космос, а пространство. Витки такой спирали разделены пустым местом, благодаря чему жидкость лучше проходит по всей ватке, меньше шанс подпалить её и вдохнуть дым вместо пара. При намотке проще, но даёт немного меньше пара. Также возможны «плевки» жидкости в рот при слишком редких кольцах, так как «жижа» может не успевать испаряться;
Койл-косичка — не совсем полноценный вид, а подтип спиралей, которые мотаются не из одной проволоки, а из двух, переплетённых между собой. Благодаря этому увеличивается площадь нагрева, а значит, вкус и пар, но также становится больше шанс втянуть вместо пара жидкость. Подходит не для всех клиров, к примеру, на Субтанк такую невозможно установить. Койлы-косички могут быть как в формате микрокойла, так и спейскойла;
Параллельные койлы — микрокойл или спейскойл, мотающийся не из одной проволоки, а из двух. Такой подход позволяет увеличить площадь нагрева, вкус и пар. В намотке сложнее, так как необходимо зафиксировать концы проволоки для равномерности;
Арт-койлы — сложные узорчатые плетения, на которые приятно смотреть и ещё приятней парить. Дают много вкуса и пара, так как площадь нагрева у них потрясающая, отлично выглядят, но очень сложны в намотке, поэтому остаются прерогативой про-вейперов.
Процесс намотки
наверхНамотка атомайзера будет продемонстрирована только на примере спейс- и микрокойла, так как создание арт-койлов слишком сложно для описания «в двух словах».
Чтобы намотать спейс- или микрокойл, понадобится такой набор инструментов:
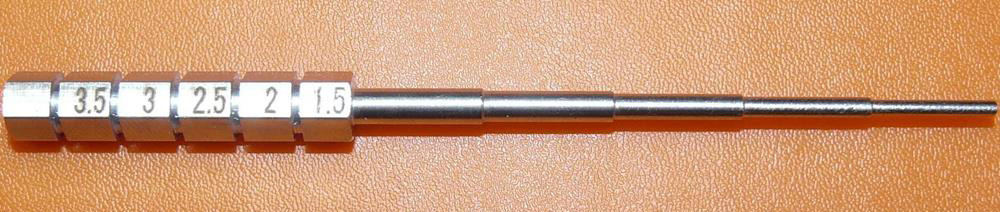
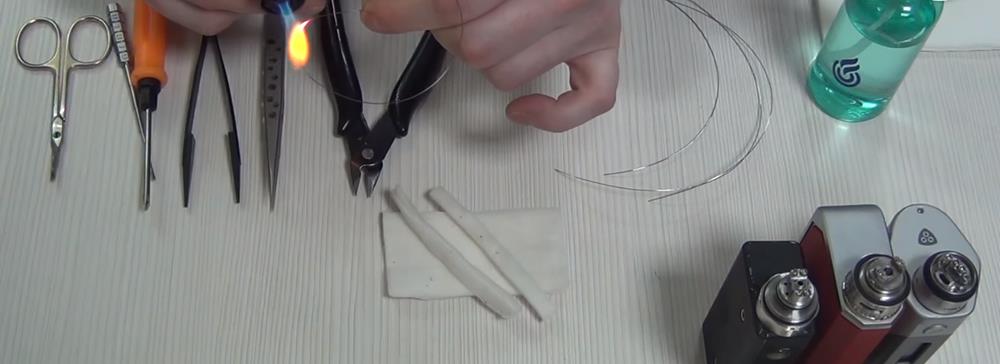
Таким образом создаются намотки на клиромайзер или дрипку. В зависимости от того, какую площадь сечения проволоки и количество колец вы выбрали, будет изменяться выдаваемый вкус и пар. Сегодня общепринятой считается намотка на 0,3 Ома, так как такое значение достигается небольшим числом колец и достаточно тонкой проволокой. Впрочем, для первых намоток подойдут любые значения.
Процесс создания более сложных спиралей, таких как Clapton, Chain и других, рассмотрен в отдельной статье .
Результат
наверхВаша спираль будет обладать различными характеристиками в зависимости от того, какие вы допустили ошибки и как расположили спираль на базе:
- температура — зависит от типа спирали и площади нагрева;
- скорость образования пара — зависит от сопротивления спирали. На значениях сопротивления выше 1,5 Ома парообразование будет относительно медленным и подойдёт для парения с сигаретной затяжкой. На значениях ниже 0,3 Ома парообразование будет быстрым, но потребуется мощный мод;
- удар по горлу (тротхит) — зависит от расположения спирали. Чем она выше относительно базы, тем жёстче ТХ, чем ниже — тем мягче;
- срок службы намотки — зависит от целого набора факторов, но основными губительными моментами являются перегрев и плохая подача жидкости. Влияние оказывает и качество самой жидкости.
Среди классических ошибок следует упомянуть неправильный расчёт сопротивления, в результате чего спираль просто «не запускается». Современные устройства частично нивелируют эту проблему, так как обладают защитами и могут работать с широким диапазоном сопротивлений. Короткое замыкание — распространённая проблема, вызванная тем, что спираль касается металлических частей базы (не считая специальных креплений). Привкус гари может проявляться при перегреве спирали, либо при недостаточной проходимости жидкости по фитилю. Протечка — результат не верно выбранного типа спирали и неправильной укладки ваты. Также возможны протечки из-за плохого закручивания деталей клиромайзера.
Насколько это выгодно?
наверхМоментальной выгоды от обслуживаемых испарителей не будет. Только долгосрочная перспектива! Понять, что намотку нужно заменить, можно по тем же признакам, что и у готового испарителя. Периодичность замены у обоих вариантов примерно равна.
Первые плоды экономии будут видны уже в первые месяцы. К примеру, испарители 0,5 Ома для Kanger SubTank стоят примерно 1300 рублей за упаковку в 5 штук. А это примерно по 520-780 рублей в месяц. Расходники же для самостоятельных намоток обойдутся в месяц примерно по 120 рублей, и это с учётом «скакнувшего» курса. Экономия почти в пять раз, но сначала вам придётся закупиться инструментами и бездарно «слить» несколько метров проволоки и ваты на обучение. Но как только вы научитесь мотать спирали, выгода этого навыка станет для вас очевидна!
В быту проведение сварочных работ требуется не часто, в отличие от производственной сферы, где сварка является неотъемлемой частью процесса. Тем не менее, при возникновении потребности варить что-нибудь, возникает также вопрос, как это сделать, с помощью какого агрегата, какие расходники нужны. Выбор способа сварки и расходных материалов напрямую зависит от того, какие материалы необходимо сварить между собой. Например, для сварки тугоплавких и цветных металлов приходится использовать сварочную проволоку, но не лишь бы какую, а под каждый случай подбирается свой вид. Нередко вопрос, как выбрать проволоку для сварки, ставит в тупик начинающего сварщика или мастера, который пользуется аппаратом недавно. В данной статье поговорим о том, какая бывает сварочная проволока и как ее подбирать под те или иные случаи.
Для сварочной проволоки самое главное - это химический состав, именно он является определяющим при выборе. Узнать его можно, прочитав маркировку на изделии отечественного производства, которая соответствует ГОСТ 2246-70 , или зарубежную маркировку по стандартам AWS .
Так как в странах СНГ производство сварочной проволоки налажено очень хорошо, разберем сначала обозначения на изделиях отечественного производства. Для начала расшифруем буквенные обозначения:
Пример: СВ-08Г2С означает,
- СВ - сварная проволока;
- 08 - массовая доля легированных элементов в составе проволоки. В данном случае проволока содержит 0,08 % углерода;
- Г - в составе есть марганец;
- 2 - не более 2 % указанного перед цифрой элемента. В данном случае не более 2% марганца;
- С - в составе есть кремний. В данном случае после обозначения «С» не стоит цифра, это значит, что кремния в составе меньше 1%, но более 0,5 %.
Пример: СВ-06Х21Н7БТ означает Сварочная проволока, в составе которой 0,06 % углерода, 21 % хрома, 7 % никеля, легированная ниобием и титаном.
Пример: СВ-08Х19Н10МЗБ означает Сварная проволока, в составе которой 0,08 % углерода, 19 % хрома, 10 % никеля, 3 % молибдена, легирована ниобием.
Иногда в маркировке по современным стандартам алюминий обозначается буквой «А».
Пример: СВ-А97 - сварочная проволока, состоящая на 99,97 % из алюминия.
Пример: СВ-АК5 - сварочная проволока, состоящая на 95 % из алюминия и 5 % кремния.
Для заказа той или иной проволоки необходимо точно указывать маркировку. К сожалению, международные стандарты не так просто прочитать, как ГОСТовские, поэтому если не нашли нужную проволоку отечественного производства, обратитесь к специалисту, чтобы он вам подобрал зарубежный аналог.
Всего существует порядка 77 марок сварной проволоки отечественного производства, которые можно разделить на 3 основных категории:
Таким образом, проволока делится по области применения: одна используется для низколегированных сталей, другая - для углеродистых, третья - для сварки цветных металлов или сварки под флюсом.
Например, рассматриваемая выше проволока СВ-08Г2С является легированной, так как в ее состав входит более 2,5 % легирующих металлов: 2 % марганца и более 0,5 % кремния.
Присадочная проволока для сварки
Сварочная проволока является так называемым присадочным материалом. В процессе сварки двух элементов проволока подводится к месту шва и плавится вместе с кромками металлов, заполняя шов. Таким образом, присадочная проволока служит материалом, который восполняет потери на разбрызгивание металла при сварке. Помимо проволоки в качестве присадочного материала можно использовать присадочные прутки и ленты.
Основное требование при выборе присадочной проволоки - у нее должен быть максимально такой же химический состав, что и у свариваемых материалов . Например, необходимо обратить внимание на содержание углерода. От количества данного элемента зависит пластичность шва. Негативными примесями считаются сера и фосфор. Для обеспечения качественного надежного шва и длительного срока эксплуатации изделия состав присадочной проволоки должен быть максимально приближен к составу свариваемых металлов.
Второе требование - температура плавления присадочной проволоки должна быть немного ниже или такой же, как у свариваемых металлов . Обратите внимание на то, когда начинает плавиться проволока, если это происходит позже, чем у свариваемых металлов, то крайне велика вероятность, что металл на свариваемых элементах прожжется. И конечно, немаловажно, чтобы плавление происходило равномерно, тогда шов получится аккуратным (без дефектов) и более прочным. Если же температура плавления подобрана неверно, это грозит появлением трещин в сварочном шве, высокой зашлакованностью шва, разбрызгиванием металла кромок, и что самое худшее - наличием скрытых полостей внутри сварочного шва.
Общие требования к присадочной проволоке:
- Толщина присадочной проволоки должна соответствовать толщине свариваемых элементов.
- Проволока должна быть чистой, без окалины, ржавчины, следов масла или краски, других загрязнений.
- Проволока должна плавиться равномерно, не разбрызгиваясь.
- Получившийся сварной шов должен быть ровным, без трещин и пор в металле.
Чаще всего присадочная проволока используется при сварке в среде защитных газов, которые обеспечивают чистый и надежный шов, защищая сварочную ванну от кислорода. В качестве защитных газов можно использовать аргон, гелий, углекислый газ или смеси аргона и углекислого газа.
Проволока для аргонодуговой сварки цветных металлов должна иметь схожий состав. Например, для сварки алюминия используется проволока СВ-97, СВ-А85, СВ-АМц или ее зарубежные аналоги ER 1100 (OK Autrod 1070 (OK Autrod 18.01)). Данные материалы устойчивы к химическому и атмосферному воздействию, применяются два сваривания изделий из чистого алюминия или его пластичных сплавов (АД1, АМц).
Проволока для сварки полуавтоматом низколегированных сталей является лидером рынка расходных материалов для сварки, так как подавляющее большинство изделий из стали относятся к данной категории. Самой распространенной присадочной проволокой является уже известная нам СВ-08Г2С, которая производится как в обычном варианте - без покрытия, так и омедненной - с антикоррозионной защитой. Использование проволоки с антикоррозионной омедненной защитой делает изделие более качественным, дуга в процессе сварки горит более устойчиво, медный наконечник расходуется медленнее.
В процессе сварки присадочными проволоками используется флюс. Вещества под названием «флюсы» дают возможность сделать структуру шва максимально идеальной, защитив тем самым металл в районе шва от преждевременного разрушения. Благодаря флюсам поверхность металла в сварочной зоне бывает ровной и гладкой, а степень растяжимости металла в зоне сварочного шва высокой. Все это делает изделие более надежным и долговечным.
В качестве флюса используются:
- Борная кислота.
- Бура.
- Окислы кремния.
- Сера.
Чаще всего присадочная проволока продается в бухтах. Перед использованием ее необходимо выпрямить и разрезать на отрезки необходимой длины. Если проволока долгое время не будет использоваться, то ее необходимо защитить, обернув катушку специальной водонепроницаемой бумагой.
Для усовершенствования процесса сварки в полевых условиях или открытых помещениях используют так называемую порошковую проволоку. Это дает возможность выполнять качественные швы, при этом затрачивая меньше сил и времени на механизацию процесса и очистку материала от брызг. Данный вид проволоки делится на два подвида: газозащитная порошковая проволока и самозащитная порошковая проволока.
Предназначена для сварки полуавтоматом и автоматом низколегированных и углеродистых сталей в среде защитного газа: углекислого газа или его смесях с аргоном.
Благодаря высокому проплавлению такую проволоку можно использовать для сварки угловых, нахлесточных и стыковых соединений практически за один проход. Преимуществами порошковой газозащитной проволоки являются низкий уровень разбрызгивания, шлаковая корка легко отделяется, высокую сопротивляемость пористости и нежелательным шлаковым включениям, стабильный струйный перенос.
Порошковые газозащитные проволоки делятся на такие типы:
Новые виды такой проволоки дают возможность достичь идеальной формы шва, низкого разбрызгивания, высокой скорости ведения шва, высокого коэффициента наплавления и малого дымления, если использовать их для сварки в защитных смесях с большим содержанием аргона.
еще называется флюсовой или просто самозащитной. Ее сердечник содержит в себе все необходимые шлакообразущие, защитные и деоксидирующие присадки. В итоге отпадает необходимость использовать баллонный газ. Это значительно облегчает задачу, так как с использованием газа связано очень много проблем и опасностей. Порошковая проволока позволяет избежать ряда хлопот с хранением, аттестацией баллонов газа, их заправкой и перемещением с места на место.
Если при обычной сварке полуавтоматом защитная ванна образовывалась с помощью газового потока, который выходил из сопла горелки, то проволока для сварки без газа позволяет создать защиту другим способом - в процессе сварки испаряется флюс, находящийся в сердечнике проволоки, и образует защитный пузырь непосредственно в месте сварки. Его невозможно смыть потоком воздуха, поэтому такие проволоки применяются для сварки на открытом воздухе при сильном ветре.
Преимущества порошковой самозащитной проволоки:
- Открытая дуга. Это дает возможность оператору следить за происходящим и перенаправлять наплавляемый металл.
- Гарантированно идеальный состав шва.
- Сваривать можно в любых положениях.
- Компактность оборудования, нет необходимости использовать баллоны с газом, а также оборудование для подачи газа и флюса.
- Специальное покрытие проволоки смазкой дает возможность противостоять механическому давлению роликов, которые подают материал в зону сварки.
Для наплавления открытой дугой используются проволоки диаметром 2,0 - 3,0 мм, а для наплавления под флюсом - диаметром 3,6 мм. Для сварки крупногабаритных изделий применяют проволоку диаметром 5,0 мм.
Технология сварки с использованием самозащитной проволоки не отличается от технологии с применением сплошной сварочной присадочной проволоки. Единственное ограничение - полуавтомат для сварки должен иметь режим No Gas.
Проволока для сварки стали
Омедненная проволока СВ-08Г2С используется для сварки трубопроводов, котлов, изделий из конструкционной стали, а также емкостей, которые в процессе эксплуатации будут находиться под высоким давлением. Также она хорошо себя зарекомендовала при работе с тонким металлом и сварке в любом положении. Устойчивость данной проволоки к растяжению находится в диапазоне 900 - 1350 МПа.
В приведенной ниже таблице указаны марки сварочной проволоки, которую можно использовать для сварки стали в условиях защиты газом - аргоном, углекислым газом или смеси этих газов.
Таблица 1. Проволока для сварки стали в защитных газах .
Проволока для сварки алюминия
Для сварки алюминия и его сплавов используется проволока, состоящая из чистого алюминия или с добавлением магния и кремния в зависимости от состава сплава, который сваривается. Чаще всего изделия бывают из алюминия (99%), алюминиево-магниевого сплава (4,8 - 6% магния и остальное алюминий) и алюминиево-кремниевого сплава (95% алюминия и 5% кремния). Для каждого из них подбирается своя проволока, это можно легко увидеть из таблицы.
Проволока для аргонной сварки алюминия используется с флюсом, который может иметь такой состав - хлористый калий 27 - 33 %, хлористый литий 9 - 12 %, хлористый натрий 42 - 48 %, фтористый калий 12 - 16 %.
Таблица 2. Проволока для сварки алюминия и его сплавов.
Сварка деталей из алюминия распространена в пищевой промышленности.
Проволока для сварки нержавейки
Сварка изделий из нержавеющей стали или жаропрочных сплавов производится с помощью полуавтомата с использованием защитного газа. Сварочная проволока изготавливается из высоколегированной жаропрочной стали. В состав сварочной проволоки из нержавеющей стали входят кремний и углерод. Кремний обеспечивает прочность сварочного шва и его качество. Углерод не дает образовываться межкристаллической коррозии.
Помимо кремния и углерода проволока из нержавейки может содержать хром и никель. Такая проволока более устойчива к коррозии. Она используется в машиностроении, пищевой и легкой промышленности, нефтепромышленности и судостроении.
Таблица 3. Сварочная проволока из нержавейки для сварки нержавеющих и жаропрочных сталей.
Использование меди в промышленности и энергетическом машиностроении связано с исключительными свойствами меди противостоять коррозии в агрессивных средах. Чем чище состав металла, т.е. в нем больше меди и меньше примесей, тем устойчивость к коррозии выше. Именно поэтому к материалам на основе меди и к присадочным проволокам предъявляются повышенные требования.
В зависимости от количества примесей различают такие марки меди:
В связи с тем, что сварные швы изделий из чистой меди должны сохранить весь комплекс физических свойств, из-за которых этот металл используется, - теплопроводность, электропроводность, коррозионную стойкость и плотность, к сварочной проволоке предъявляются крайне строгие требования. А в процессе сварки шов не должен загрязняться примесями.
Сварочная проволока для меди изготавливается из электролитической меди, а в процессе сварки может использоваться флюс из буры 48 - 53 %, хлористого натрия 32 - 38 %, борной кислоты 10 - 14 %.
Таблица 4. Проволока для сварки меди.
Для сварки никеля хорошо подойдет проволока, легированная такими металлами, как марганец (не более 2%), кремний (не более 0,8 %), магний (не более 0,3 %) и титан (не более 0,1 %). Марганец необходим для раскисления и связывания серы, кремний делает металл более жидкотекучим, магний связывает те остатки серы, которые остались после марганца. Диаметр проволоки для сваривания никеля желательно выбирать равный половине толщины металла свариваемых изделий.
Чугун же трудносвариваемый металл, так как велика вероятность появления трещин в сварном шве. Выходом из ситуации стало использование для сварки проволок, покрытых цветными сплавами, или предварительный подогрев заготовок перед свариванием и использование порошковых проволок.
Таблица 5. Проволока для сварки чугуна и сплавов никеля.
Проволока для сварки титана
Для сварки титана используется холоднотянутая проволока из листового металла. Состав должен быть максимально приближен к составу основного материала. Чаще всего это присадочная порошковая проволока марки ППТ-1 и ППТ-3. Сама технология сварки титана подразумевает использование аргонодуговой сварки и неплавящегося вольфрамового электрода. Расход проволоки составляет 1,2 - 1,5 м на каждый погонный метр шва.
Диаметр сварочной проволоки
Диаметр присадочной проволоки подбирается в зависимости от толщины металла в свариваемых заготовках. Так если толщина изделия 3 - 5 мм, то берут проволоку 2 мм, если толщина 5 - 16 мм, то используют проволоку диаметром 3 - 4 мм. Для более толстых листов 7 - 25 мм можно использовать проволоку 7 мм толщиной.
Для сварочных полуавтоматов выпускается проволока в таких диаметрах: 0,6 мм, 0,8 мм, 1 мм, 1,2 мм, 1,6 мм.
Проволока для сварки с помощью электродов и присадочных прутков - 1,6 - 5 мм.
Самый широкий диапазон сварочной проволоки в категории порошковых проволок - 0,6 - 6 мм.
Помимо толщины изделия на требуемый диаметр сварочной проволоки также влияет сила тока, которая необходима для сварки в конкретном случае. Посмотреть, какие диаметры проволоки необходимо в том или ином случае можно в таблице ниже.
Таблица 6. Диаметр сварочной проволоки в зависимости от силы тока.
Выбор сварочной проволоки - очень ответственная задача. Если предоставленные таблицы все равно не помогли вам разобраться в вопросе, какую проволоку использовать, то лучше обратитесь за помощью к специалисту.
Поскольку полуавтоматы для сварки сейчас довольно востребованы, это позволило создать широкий рынок производства сварочной проволоки для полуавтомата. Правильный выбор проволоки позволяет существенно повысить производительность, а также качество самой сварки и сварного шва. Дополнительно повышается и безопасность, что тоже немаловажно для квалифицированных сварщиков.
Типы и маркировка проволоки для сварки
Сварочная проволока для полуавтоматов используется как плавящийся электрод при проведении сварочных работ на полуавтомате.
Существует около 77 марок проволоки для сварки, качество и состав которых регулирует ГОСТ 2246-70. Этому стандарту полностью соответствует выпускаемая холоднотянутая проволока из низкоуглеродистой стали, легированной, а также высоколегированной стали.
Сварочная проволока для полуавтоматов подразделяется по своему назначению на:
- непосредственно для сварки;
- для изготовления электродов (дополнительное обозначение Э).
Низкоуглеродистая и легированная проволоки сортируются по виду обработки поверхности на неомеднённую и омеднённую (О).
Несмотря на большое количество различных марок проволоки для сварки полуавтоматом, в производстве и строительстве широко используют для работы всего несколько. Остальные – это марки специальные, или узкопрофильные. При изготовлении к ним предъявляют особенные требования. Такая проволока предназначается для проведения сварочных работ при строительстве научных комплексов и лабораторий, объектов атомной промышленности и для других современных отраслей промышленности, которые используют высокие технологии.
В настоящее время применяются технологии, позволяющие проводить сварку полуавтоматами не только в нейтральной среде защитного газа, но и при помощи проволоки, под слоем флюса. Тип применяемой проволоки, её диаметр и марка всегда зависят от толщины и химического состава конструкций и деталей, подлежащих сварке. В связи с этим, сварочная проволока для полуавтоматов делится на три основные категории:
- низкоуглеродистая – такие марки проволоки, как Св-08АА, Св-08, Св-10ГА, Св-08ГА и Св-10Г2;
- легированная – марки проволоки Св-12ГС, Св-08ГС, Св-10ГН, Св-08Г2С, а также Св-08ГСМТ и др.;
- высоколегированная – марки Св-10Х11НВМФ, Св-12Х11НММФ, Св-Х13,Св-20Х13 и др.
Если знать маркировку, то одного взгляда на название будет достаточно, чтобы узнать её состав. Таким образом, название Св-08Г2С говорит о следующем:
Аббревиатура Св обозначает, что данная проволока сварочная. Буквы и цифры, идущие следом, рассказывают о содержании составляющих элементов в той или иной проволоке. Далее, цифры 08 говорят о массе углерода в сотых долях процента, в этом случае здесь 0,08%. Г – сообщает о том, что в состав проволоки входит марганец, следующая цифра 2 говорит о двухпроцентном его содержании. Буква С указывает на кремний в составе проволоки, если далее цифр нет, то его содержание не превышает 1%.
В некоторых случаях необходимо знать дополнительную маркировку проволоки:
А – стоящая в конце маркировки, означает, что эта проволока с уменьшенным содержанием вредных веществ, вроде серы или фосфора, а две буквы (АА) говорят о том, что проволока содержит минимум вредных примесей, а сама проволока сделана из металла высокой очистки. Кроме того, внутри маркировки А показывает наличие в составе азота.
Х и Н – (хром, никель), в основном используются как легирующие добавки, в том случае, если изготавливается сварочная проволока для нержавейки.
Остальные элементы, встречающихся в маркировках:
В - вольфрам;
Т - титан;
Ю - алюминий;
Ф - ванадий;
Б - ниобий;
Д - медь;
М - молибден;
С - кремний;
Ц - цирконий.
Можно выделить несколько самых известных производителей проволоки для сварки. Это Компания ООО «Петромет», выпускающая такие популярные в нашей промышленности марки проволоки, как Св-08ГСНТи Св-08Г2С, Св-08ГНМ, Св-08ХМ и др. ООО «Свармонтажстрой», производство которого основано на ряде иностранных технологий и качество выпускаемых изделий соответствует основным международным нормам. Московский производитель ООО «Велд – Метиз».
Диаметры сварочной проволоки
Номинальные диаметры проволоки применяемой для сварки полуавтоматом имеют размеры от 0,3 мм до 12 мм. Всего существует 17 стандартных диаметров.
Предварительно, при сварке автоматом выбирают проволоку диаметром до 5 мм, а при полуавтоматической, механизированной – до 2 мм, в основном её диаметр зависит от толщины металла.
Для достижения требуемого качества сварочного шва, при сварке деталей и конструкций из легированных и высоколегированных сталей, химический состав самой проволоки обязательно должен быть таким, чтобы в получаемом шве содержание углерода ограничивалось 0,10 – 0,12%, а кремния было менее 0,5%.
Для сварки специализированных сталей применяются высоколегированные аустенитные и ферритные сварочные проволоки. Однако аустенитная высоколегированная сварочная проволока для полуавтоматовпосле волочения нагартовывается (нагартовка – наклёп) и становится более жёсткой, а её пластичность снижается. В связи с этим подача проволоки такого малого диаметра от 2 – 3 мм по шлангам при сварке полуавтоматом, облегчается, в отличие от подачи проволоки большего диаметра.
Сварка с применением газовой смеси отличается лучшими техническими показателями. Поэтому в настоящее время повсеместно используют смесь углекислого газа и нейтрального аргона, имеющую процентное соотношение – 75-80% Ar и 20-25% CO2.
Контроль расхода сварочной проволоки
В процессе сварки на полуавтомате, необходимо вести учёт расхода проволоки для сварки и газовых смесей. Это обеспечивает экономию расходных материалов на производстве и ведёт к снижению себестоимости самих работ.
На расход проволоки для сварки оказывают влияние такие показатели как:
- химический состав металла;
- диаметр и качество самой проволоки;
- данные технических характеристик рабочего полуавтомата для сварки;
- проведение сварки в среде нейтрального газа.
Во многих случаях, расход используемой сварочной проволоки считается до 1,5 % от веса всей конструкции. А вес проволоки превышает вес наплавляемого материала до 6%, так как имеют место угар и отходы.
Нормы расхода определённых марок проволоки на метр сварочного шва определяются по формуле М = НР ∙ КР. (где М – масса наплавляемого металла, напрямую зависящая и от металла, и от вида сварочного шва). КР – коэффициент расхода используемой проволоки (значение берётся из таблиц).
Исходя из данной формулы рассчитывают потребность в сварочной проволоке не только для конкретного вида работ, но и для всего предприятия в течение времени.
Современные механизмы и скорость подачи сварочной проволоки
Сварочные полуавтоматы классифицируют следующим образом:
- для сварки изделий в защитных газах;
- для сварки с помощью порошковой проволоки;
- для выполнения сварки под флюсом;
- универсальные.
Полуавтоматы для сварки с применением защитных газов оборудованы специальным клапаном, прекращающим подачу рабочего газа по окончании сварки.
В полуавтоматах для сварки под флюсом всегда есть горелка с воронкой. Осуществляется более мощная подача проволоки, чем на другом оборудовании, поскольку для этой сварки необходима проволока большого диаметра.
Сварочные полуавтоматы разделяют на бытовые, полупрофессиональные и профессиональные, в зависимости от силы тока и длительности работы самого аппарата. А также бывают передвижными, стационарными и переносными. Промышленные полуавтоматы изготавливают только для работы в режиме трёхфазного тока. Швы, получаемые при использовании в работе таких аппаратов гораздо более качественные и ровные.
Полуавтоматы для сварки современной порошковой проволокой снабжены специальным устройством подающих роликов, чтобы не допустить деформации рабочей проволоки.
Универсальные полуавтоматы укомплектованы вспомогательными приспособлениями (сварочными горелками, роликами для подачи проволоки и др.), что даёт возможность с успехом использовать их для различных видов сварки.
К механизму подачи проволоки к горелке относятся – электродвигатель, редуктор и, конечно, подающие ролики. Вид подающего устройства (относительно газовой горелки), может быть тянущий, толкающий и универсальный. При подаче проволоки устройством толкающего типа, подающие ролики находятся у самого шланга сварочной горелки и равномерно толкают проволоку непосредственно в канал горелки. Используется всегда при сварке стали.
С помощью подачи проволоки на полуавтомате механизмом тянущего типа проволока попадает в канал горелки. Это придаёт ей дополнительный вес, но тем не менее, такой механизм часто устанавливают в полуавтоматах для сварки алюминия. Сварочная проволока для полуавтоматов служит не только для улучшения качества шва, но и непрерывности сварочных работ. Подачу тянуще – толкающего типа применяют для сварки алюминия в случае значительного удаления основного сварочного механизма от места сварки.
Скорость подачи проволоки необходимо настраивать для каждого случая и регулировать по ходу работ. Основную регулировку скорости подачи выполняет коробка передач и комплект шестерён. В таком случае приводом служит трёхфазный асинхронный двигатель. Недостатком данной регулировки скорости является трудность подбора необходимого режима для сварки. Особенно при работе с тонким металлом.
Плавное регулирование необходимой скорости подачи проволоки очень малого диаметра достигается при использовании в работе двигателя постоянного тока, путём плавного изменения числа оборотов головки двигателя. Скорость подачи может доходить до 150 м/ час.
При настройке скорости подачи важна толщина металла, состав и диаметр выбранной сварочной проволоки. Получить качественный сварочный шов возможно только при тщательной регулировке скорости путём нескольких пробных сварок.
Перемотка атомайзера: основы
Большинство начинающих вейперов предпочитают покупать новые испарители и опасаются лишний раз вмешиваться во “внутренний мир” своего нового гаджета. С опытом благоговение и страх проходят, предпочтения меняются и на первый план выходят аргументы в пользу самостоятельной перемотки атомайзера :
Можно создавать собственные спирали с любым желаемым сопротивлением, от очень низкого в 0,1 Ом до высокого 1,8 Ом.
Собственноручная намотка спирали испарителя для электронной сигареты дает заметную экономию. Расходные материалы для обслуживания атомайзера стоят гораздо дешевле, чем фабричные сменные “головы”.
Перемотка атомайзера своими руками позволяет добиваться определенных параметров парения: количества пара, насыщенности вкуса, силы удара по горлу и т.д.
А еще частота и качество перемотки атомайзера прямо пропорциональны чувству собственной важности среди других вейперов. А это, между прочим, весомая причина в любой субкультуре.
Основы намотки спирали для чайников
Разумеется, мы будем наматывать спираль для электронной сигареты, а не для кухонной техники. Но если прежде вам не приходилось перематывать атомайзер, то начнем с азов. Итак, вот что вам понадобиться для самостоятельного обслуживания испарителя:
Обслуживаемый атомайзер, то есть оснащенный базой для установки спирали или даже нескольких. Чтобы купить обслуживаемый атомайзер в интернет-магазине, ориентируйтесь на пометки в его описании: RBA (rebuildable atomizer), RTA (rebuildable tank atomizer) или RDTA (rebuildable dripping tank atomizer, он же - дрипка с баком).
Инструменты для намотки спирали. Те, кто уже набил руку в перемотке атомайзеров , обходятся гвоздем подходящего диаметра, ножницами и знанием законов Ома. Если вы пользуетесь обслуживаемым атомайзером недавно, вам пригодится, как минимум, специальный стержень для намотки с разными диаметрами (народное название - “моталка”), кусачки, керамический пинцет (не проводит электричество) и калькулятор намотки (онлайн или в мобильном приложении).
Материалы для намотки спирали и создания фитиля. Вате для фитиля мы уже посвятили отдельную статью, а здесь подробно поговорим о видах проволоки для электронных сигарет . Таких видов несколько: нихром, кантал (синоним - фехраль), нержавеющая сталь, никель, титан. Их отличает удельное сопротивление материала, прочность и стоимость.
На вейп-форумах ведутся горячие споры на тему: что лучше, нихром или кантал . Вскоре вы станете не только читателями, но и участниками тих дискуссий. А пока позвольте выразить наше мнение на этот счет и аргументировать его несколькими фактами.
Нихром, кантал и другие: свойства и отличия
Стальная, нихромовая и канталовая проволока одинково широко используются в вейп-среде для намотки спиралей. Другое дело, что мнения парильщиков насчет лучшей проволоки разделились. У каждого материала есть свои плюсы и минусы - это правда. Вот объективная информация о них:
Нихром - сплав никеля и хрома с незначительными примесями других металлов (опционально). Нихромовая проволока довольно мягкая и гибкая, долго не чернеет и недорого стоит.
Кантал - сплав железа, хрома и алюминия. Если встретите материал под названием фехраль , знайте, что это тот же слав (FeCrAl). Разные наименования возникли из-за конкуренции производителей. Кантал - зарегистрированное название фехраля, не более того. Канталовая проволока не содержит никеля, пружинит и менее долговечная. Зато стоит кантал дешевле нихрома.
Нержавеющая сталь тоже используется для намотки спирали. Стальная проволока дешево стоит и долго служит, но наматывается плохо.
Никель, титан - проволока из этих материалов выдерживает большие температуры и считается “элитным” материалом для намотки. Цена у нее соответствующая, поэтому в данной статье, предназначенной для начинающих, мы не будем останавливаться на титане и никеле.
Из всех перечисленных материалов наибольшей популярностью пользуются нихром и кантал , потому что обладают соотношением характеристик, лучшим среди остальных. И все равно одни вейперы считают, что лучше нихром, другие - что лучше кантал. Так все же, что лучше: нихром или кантал?
Выбор между нихромом и канталом
Как обычно в таких случаях, однозначного ответа на вопрос нет. Выбор зависит от желаемого удельного сопротивления проволоки, которое, в свою очередь, определяет настройки мода и стиль парения (количество пара, сила вкуса, удар по горлу и т.д.). Модель атомайзера тоже играет большую роль. Учитывайте все эти отличия при выборе проволоки для спирали:
Кантал обладает большим сопротивлением по сравнению с нихромом.
Нихром обладает меньшим сопротивлением, чем кантал. Поэтому со спиралью из нихромовой проволоки можно получить больше мощности боксмода.
Кантал пружинит и “упрямится” во время намотки спирали. Это можно устранить путем предварительного прогрева проволоки.
Нихром не содержит железа, склонного к образованию ржавчины. Это продляет срок службы нихромовой спирали.
Кантал - более тугоплавкий материал, нежели нихром. Это значит, что прожиг спирали из канталовой проволоки происходит проще и сопряжен с меньшим риском пережечь спираль.
Нихром лучше проводит тепло, а значит, спираль из этого материала быстрее разогревается и быстрее остывает, устойчивее к перепадам температуры.
Названные свойства проволоки из нихрома или кантала для электронных сигарет приведены для того, чтобы продемонстрировать вам разницу между ними. При этом, как видите, здесь нет категоричных достоинств и недостатков: те или иные качества уместны в разных ситуациях. Например, мягкий и податливый нихром любят авторы сложных “художественных” намоток. Кантал предпочитают новички, потому что он дешевле.
Попробуйте для начала купить недорогую канталовую проволоку и сделать свою первую самодельную спираль. Со временем вы войдете во вкус и выясните, что означает маркировка проволоки, как это влияет на ее свойства и, в конечном итоге, на свойства парения. Это поможет вам сориентироваться в теме перемотки атомайзера , а мы еще вернемся к ней для обсуждения толщины проволоки, формы спирали и многого другого.
Статья написана главным образом для начинающих, если вы уже перемотали не одну сотню спиралей – то эта статья вам не нужна, так как ничего нового вы тут не узнаете.
Рассмотрим несколько самых распространённых вопросов с которыми сталкиваются начинающие парильщики, для начала стоит решить какую проволоку приобрести, диаметр и тип, нихром или кантал.
Выбирать тип проволоки нужно в первую очередь исходя из того, куда вы её собираетесь устанавливать, если это генезис танк, или любой другой танк где в качестве фитиля используется нержавеющая сетка – тогда приобретайте только кантал. Если же в качестве фитиля используется кремнеземный шнур, супернить, бамбуковая пряжа – то можно использовать как кантал так и нихром. Субъективно – на кремнеземе, лучше использовать нихром, так как он быстрее нагревается, ч то важно на не слишком мощных девайсах, чтобы избавиться от эффекта пружины – перед тем как мотать спираль, прожгите проволоку горелкой.
Различия между типами проволоки заключаются в составе сплава:
Нихром - общее название группы сплавов, которые состоят из Никеля и Хрома (НиХром), в зависимости от марки, может содержать и другие металлы, для улучшения тех или иных характеристик.
Кантал – зарегистрированная торговая марка, принадлежащая компании Sandvik Materials Technology, под этим названием компания Sandvic выпускает сплав состоящий из железа, хрома и алюминия, у других производителей проволока из такого же сплава называется Фехраль (FeCrAl).
Оба сплава используются в качестве нагревательных элементов во всяких электро приборах – утюгах, фенах, электропечах для обжига и сушки, и так далее, кантал и нихром обладают несколько разными свойствами. Кантал – нагревается равномерно, и практически не имеет пружинного эффекта во время намотки. Нихром – чуть более устойчив к агрессивным средам, поэтому не так быстро чернеет, более мягкий, легче гнётся.
В зависимости от состава сплава, проволока может иметь маркировку, к примеру нихром может маркироваться как – Cr20Ni80,Cr30Ni70,Cr20Ni35,Cr20Ni30,Cr15Ni60, цифровая часть обозначает процентное соотношение металлов в сплаве, например Cr20Ni80 означает что сплав на 20% состоит из хрома и на 80 из никеля. Проволока также бывает нескольких типов к примеру Kanthal A1 и Kanthal D, различия между ними в рабочих температурах, A1 более жаростойкий, но в случае с электронными сигаретами особой разницы нет, если имеется выбор – приобретайте A1.
По поводу сопротивления и диаметра проволоки, я не буду забивать вам голову всякими формулами из учебника физики, так как сам их толком не помню, принцип здесь довольно прост, чем толще проволока – тем меньше у неё сопротивление. Например – сделав пять витков нихрома проволокой с диаметром 0.10 мм, вы получите спираль с сопротивлением 2.2 Ом, а сделав пять витков на проволоке с диаметром 0.20 мм – получите 1.2 Ом. Нередко сталкиваюсь с тем, что следом за первой ЕГОшкой парильщик покупает какой нибудь варивольт, и пытается парить его на максимальной мощности. Особого смысла в этом нет, варивольт или вариватт даёт возможность подстроить вольтаж под сопротивление спирали, то что у вас есть опция в шесть вольт не значит что любой атом будет хорошо работать на таком вольтаже.
Взгляните на таблицу:
Зелёным цветом выделена зона комфортного парения, в первой верхней горизонтальной колонке – указано сопротивление атомайзера, в первой слева вертикальной колонке – вольтаж, в ячейках таблицы значения в ваттах.
Как видим шесть вольт уместно использовать только на спиралях с сопротивлением 3.0-3,5 Ом. Для большинства варивольтов оптимальное сопротивление намотки 1.6-2.2 Ом, намотку с сопротивлением меньшим чем 1.5 ом делать не стоит т.к. в большинстве варивольтов имеется защита LR атомайзеров – устройство не подаст напряжение на спираль если её сопротивление меньше 1.5 ом, чтобы случайно не спалить атом. Те же кто использует механические моды – подгоняет сопротивление спирали под вольтаж аккумулятора, намотки для мех-модов чаще всего имеют сопротивление от 0.8 Ом до 1.2 Ом.
Как правило диаметр сечения проволоки указывается в AWG, это американская система калибровки проводов в которой всё перевёрнуто с ног на голову, так меньшее число AWG соответствует более толстому диаметру проволоки. Чтобы перевести AWG в миллиметры и обратно используйте таблицу:
Наиболее распространённые диаметры для нихрома – 0.20 мм, кантал – 0.30 мм, проволоку с диаметром 0.10 и 0.15 мм приобретают для намотки косичкой, при этом несколько нитей сплетаются в одну, за счёт чего увеличивается площадь нагрева и КПД соответственно:
Хорошей площадью нагрева и высоким кпд обладает так называемая “лапша” – лента из кантала диаметром 0.10 х 0.50 мм, она незаменима на генезисах и других атомайзерах использующих нержавеющую, стальную сеть в качестве фитиля:
Её так же можно использовать с бамбуком и кремнеземным шнуром:
Надеюсь представленная тут информация поможет вам сориентироваться, удачи!